Abstract
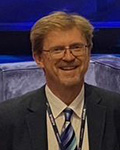
Influence of radiation on Self-Lubricating Polymer
(used as cages for bearings)
Andreas Merstallinger1, Zoltan Simon1, Manuel Hochrainer2, Christoph Tscherne3, Cristina Paul4
1 AAC GmbH
2 Ensinger Sintimid GmbH
3 Seibersdorf Labor GmbH
4 ESA/ESTEC
Abstract
Mechanisms belong to critical components in space. This applies to the Large Deployable Reflectors (LDR) itself as well as to deployable arms (ABDM) needed to place the reflector in appropriate distance to the spacecraft. Also pointing mechanisms for solar arrays (SADM) or antennas (APMs) require a reasonable variety of bearings, even down to diameters of few millimetres. The most common way of their lubrication is by fluids. However, that limits their temperature range as the fluid would evaporate at too high temperatures of freeze when being too cold. It would ease the thermal management and decrease the related costs by reduction of mass, wiring, if fluid lubrication could be replaced by solid lubrication. Hereby, bearings may be operated in much wider temperature ranges from almost +160°C down to even cryogenic temperatures without contamination by outgassing.
Therefore, a new material based on PTFE was developed. The primary task was to develop a formulation that offers proper lubrication combined with sufficient tribological lifetime. However, tribological performance and mechanical stability of polymers depend strongly on the radiation environment. In typical mechanisms, the lubricating item (a cage) is not exposed to space, it is hidden by the housing and by bearing components made of steel. Hence, ATOX and several radiation types (UV, alpha, beta) can be ignored. Only X-ray affects those parts. Especially when using PTFE this may become a critical issue [1]: in a range of 1-10 MRad such material can already degraded, e.g. they may become brittle. Within the A3Lub2-project an application for LEO requires a stability after a dose of 1MRad being representative for a life of 15years.
The presentation will give an overview on the verification approach, i.e. material tests were done before and after exposure to radiation. Some results of those tests will be presented. Finally, their implication on the performance of the bearings will be discussed.
References
[1] Radiation effects design handbook.pdf (NASA, 1971).
Acknowledgments
The presented work was part of the ESA-project “A3Lub2”, contract No. 4000134713/21/NL/MG/idb, finalisation 2024.